MARINE GUIDANCE NOTE
Published 15 October 2024
MGN 578 (M) amendment 2 use of overside working systems on commercial yachts, small commercial vessels and loadline vessels
Summary
This notice provides guidance on the use of overside working systems for working over the side and at height on yachts, small commercial vessels and loadline vessels.
Shipowners have a responsibility to ensure that;
- new systems comply with the current BS/EN standards
- systems are installed as per manufacturer's instructions;
- existing systems have been checked to an equivalent standard and
- maintenance is carried out according to manufacturer's instructions
Amendment 1 reflects updated references and guidance for overside working systems.
Annex 1 lists the following regulations which are relevant to overside working.
Annex 2 gives details of the testing and operating procedures.
Annex 3 contains the requirements for single person systems.
1. Introduction
1.1 The use of overside working systems are now considered standard on vessels especially commercial yachts. Such installations allow crew members to work outside conventional guardrails for cleaning and maintenance purposes.
1.2 Most overside working systems consist of one or a combination of the following;
- "rail and car" or "rail and trolley" systems comprising of two travellers, cars or trolleys linked in tandem that can be separated, if necessary, into independent units. These cars are fitted to a metal rail which allows them to glide along it and to which support harnesses are attached
- harnesses, lanyards, fall arresters, energy absorbers and similar devices
- single anchoring points, pad eyes and eye bolts.
1.3 Traditionally many of the early "rail and car" systems were designed for the sole purpose of sail handling and not for supporting crew members working over the side of the vessel. It is a requirement of the merchant shipping and fishing vessels (health and safety at work) (lifting operations and lifting equipment) regulations 2006 (S.I. 2006/2184) that equipment which is used for lifting persons must be designed for the purpose. It is not acceptable to use a "rail and car" system designed solely for sail handling for the purpose of supporting crew members working over the yacht's side.
2. Installation
2.1 A newly installed overside working system, anchoring point and attachment should be tested, certified and approved to a recognised standard for fall protection equipment (EN 795:2012; Type D (or any subsequent revision) and is marked with the UK Conformity Assessed marking (UKCA) or to an equivalent standard if manufactured elsewhere. EN 795:2012; Type D revises, expands upon and replaces EN 795:1996, referred to in MGN 578(M) Amendment 1.
2.2 More information on these requirements is contained in Annex 2.
2.3 EN795:2012 is supported by a Technical Specification - CEN TS 16415: Personal Fall Protection Equipment Anchor Devices Recommendations for anchor devices for use by more than one person simultaneously; which addresses multiple simultaneous users.
2.4 The requirements for single person systems are contained in Annex 3.
2.5 An overside system should not be used, unless specifically designed and certified by the manufacturer for that purpose. Including any conditions attached to its use, while supporting crew working overside or at height.
2.6 It is essential that specific manufacturer's instructions are followed e.g. which fastenings to be used, torque limits of fastenings, bending limitations on the rail etc. Full details of the installation including method of anchorage and supporting technical documentation (fixing certification) must be issued on completion of every installation.
3. Operation
3.1 Prior to permitting the work the employer should ensure that all alternative means for carrying out the work are considered.
3.2 Before use of the equipment the employer should ensure that:
- 3.2.1 the manufacturers' instructions are read and understood by the persons who will be using the equipment;
- 3.2.2 a risk assessment is carried out and an appropriate rescue plan developed to recover persons who fall into the water; and
- 3.2.3 crew members are competent to use the equipment and are aware of any conditions relating to its use and their safety.
3.3 Overside working systems must not be used whilst the vessel is underway.
3.4 These systems are designed to be used with the appropriate Personal Protective Equipment(PPE) e.g. harnesses, lanyards, fall arresters and other devices.
3.5 On systems where one of the travellers is fitted with a locking device, the device which locks the traveller in position along the track rail must only be disengaged from the track rail while the user is changing position. Once the user is in position, the locking device shall be re-engaged to hold the car or trolley in position and limit the user's movement along the track rail.
3.6 The user must NEVER rely on only one attachment point for personal protective equipment. The working harness should be attached to one traveller and a fall arrestor or other safety device to the other. A third traveller could be used to attach work tools.
3.7 More guidance can be found in the Code of Safe Working Practices for Merchant Seafarers (COSWP) Chapter 8; Personal Protective Equipment and Chapter 17; Work at Height.
3.8 The use of systems for overside work that do not meet the requirements of either paragraphs 2.1 and 2.2 above or fail to provide instructions in the use of such equipment in accordance with paragraph 3.1 above, could potentially place the employer of the crew, and also the master, in breach of their obligations under relevant Merchant Shipping Health and Safety legislation and render them liable to prosecution and a fine for non-compliance. Further information on relevant legislation is set out in Annex 1.
3.9 The overside working system should never be used to hold fenders or tenders alongside the vessel, as this could lead to dynamic loading which could lead to damage or failure of the system.
4. Maintenance
4.1 Where systems meeting the requirements of either paragraphs 2.1 or annex 2 are used for overside work, relevant information regarding the maintenance and testing of such systems should be obtained from the system manufacturer. Such information is to be in written form and a copy of it is to be kept on board the vessel to which it applies.
4.2 Anchor devices which have been installed and certified to EN 795:1996 are still valid.
4.3 Existing anchor devices conforming to and pre-dating EN 795:1996 can continue to be tested and certified to this standard. Existing anchor devices which have been modified or changed must meet the standards stated in 2.1. Uncertified or decommissioned systems are to be assessed on a case by case basis and should not be used until the arrangements have been approved.
4.4 Where any overside working systems, anchoring point or attachment has been subject to damage, overloading or a dynamic loading equivalent to fall arrest, the system should be retired from service and subject to a full review by a representative of the manufacturer, to confirm the system remains fit for continued use.
4.5 All overside working systems, anchoring point and attachments should be suitably marked with the UKCA mark.
4.6 More information on the testing of these systems is contained in annex 2.
More Information
Seafarer Safety and Health Branch
Maritime and Coastguard Agency,
Bay 2/17
Spring Place,
105 Commercial Road,
Southampton,
SO15 1EG.
Tel : +44 (0)203 81 72250
e-mail: seafarersafety@mga.gov.uk
Website: www.gov.uk/mca
General Inquiries: infoline@mcga.gov.uk
Please note that all addresses and telephone numbers are correct at time of publishing.
ANNEX 1
MERCHANT SHIPPING LEGISLATION RELEVANT TO OVERSIDE WORK
The following provisions of Merchant Shipping Legislation are relevant to overside work. However only the main points especially relevant to the use of selection of rail and trolley systems are listed. In order to meet the requirements of the legislation completely it will be necessary to comply fully with all the requirements of this legislation.
1. Merchant Shipping and Fishing Vessels (Health and Safety at Work) Regulations 1997 (S.I. 1997/2962) as amended
- 1.1 Under regulation 5 of the merchant shipping and fishing vessels (health and safety at work) regulations 1997 (the "general duties regulations") guidance on which is contained in MGN 636 (M) amendment 3, a general duty is placed on the shipowner and employer to ensure, so far as practicable, the health and safety of seafarers, workers and other persons on board a UK registered vessel. In meeting this requirement they are required to undertake a risk assessment to determine whether any risks to health and safety will, or potentially could, arise in the normal course of their activities or duties. Where any such risks, or potential risks, are identified the shipowner or employer is required to take appropriate measures to either remove such risks entirely or, where that is not possible, reduce those risks as far as reasonably practicable. It is for the shipowner or employer to decide what measures are taken to reduce any risks.
The regulations covered by sections 2 to 4 below apply to shipowners in respect of seafarers as well as to employers in respect of workers.
2. Merchant Shipping and Fishing Vessels (Provision and Use of Work Equipment) Regulations 2006 (S.I. 2006/2183)
- 2.1 In addition to the provisions of the General Duties Regulations referred to above, regulation 6 of the Merchant Shipping and Fishing Vessels (Provision and Use of
Work Equipment) Regulations 2006, guidance on which is contained in Marine Guidance Note MGN 331 (M+F) requires any employer to ensure that all work
equipment made available to workers on the ship:
- a. is suitable for the work to be carried out; or
- b. is properly adapted for that purpose; and
- c. may be used by workers without impairment to their health and safety.
- 2.2 When selecting work equipment the employer is required to take into account the conditions under which the work is to be undertaken and the characteristics of the work as well as having regard to any risks to the health and safety of workers arising from the use of that work equipment.
- 2.3 The employer must also ensure that any work equipment is used only for operations, and under conditions, for which it is suitable.
- 2.4 "Suitable" in this context means suitable in any respect which it is reasonably foreseeable will affect the health and safety of any worker.
- 2.5 Any work equipment to be used by workers must be maintained in accordance with the manufacturer's instructions, in an efficient state, in proper working order and in good repair.
Regulation 6
3. Merchant Shipping and Fishing Vessels (Lifting Operations and Lifting Equipment) Regulations 2006 (S.I. 2006/2184)
- 3.1 Should the use of the overside working systems involve lifting or lowering of any worker the provisions of the Merchant Shipping and Fishing Vessels (Lifting Operations and Lifting Equipment) Regulations 2006. The guidance lifting operations contained in Marine Guidance Note MGN 332 (M+F) Amendment 3 will also apply.
- 3.2 Under these Regulations the employer is required to ensure that all lifting equipment is of adequate strength and stability having regard in particular to the stress induced at its mounting or fixing point.
- 3.3 In addition the Regulations provide that, except in exceptional circumstances, no lifting equipment shall be used for lifting persons unless it is designed for the purpose.
4. Merchant Shipping and Fishing Vessels (Health and Safety at Work) (Work at Height) Regulations 2010 (S.I. 2010/332)
- 4.1 Guidance on The Merchant Shipping and Fishing Vessels (Health and Safety at Work) Regulations 2010 guidance to which is contained in Marine Guidance Note MGN 410 (M+F), requires employers to ensure that work equipment used for work at height is the most suitable to ensure and maintain safe working conditions for worker using that equipment.
- 4.2 The Regulations also require the employer to select work equipment which is appropriate to the nature of the work to be performed and is appropriate to foreseeable loads and stresses. In addition specific "Requirements for Rope Access and Positioning Techniques" are set out in Schedule 3 to the Regulations.
ANNEX 2
PROTECTION FROM FALLS FROM HEIGHT - ANCHOR DEVICES - REQUIREMENTS AND TESTING
Anchor devices or fixed rail devices fitted on vessels must comply with EN 795:2012 (or subsequent revision) and are typically Type A or Type D anchoring devices.
Tests should be carried out on a sample of the medium to which the Type A or D anchor devices are attached. In the case of traveller and bar each test should be repeated at the extremity and intermediate anchor and at a joint.
A static test with a weight of 12kN should be applied for a period of 3 minutes. The device should suffer no permanent deformation of more than 10 mm. Where the medium to which the anchor device is to be attached is non-metallic and where evidence of durability is not provided by the manufacturer, the static test weight shall be 18kN.
A dynamic test consists of a 100 kg mass being dropped so that it generates a fall-arrest load of 9kN. The anchor device shall not release the test mass. Increase the test mass to 300 kg for 3 minutes. The mass is held clear of the ground
Precise descriptions of the required tests can be found in EN 795:2012 (or subsequent revision).
Diagram 1 is an example of a traveller showing its construction.
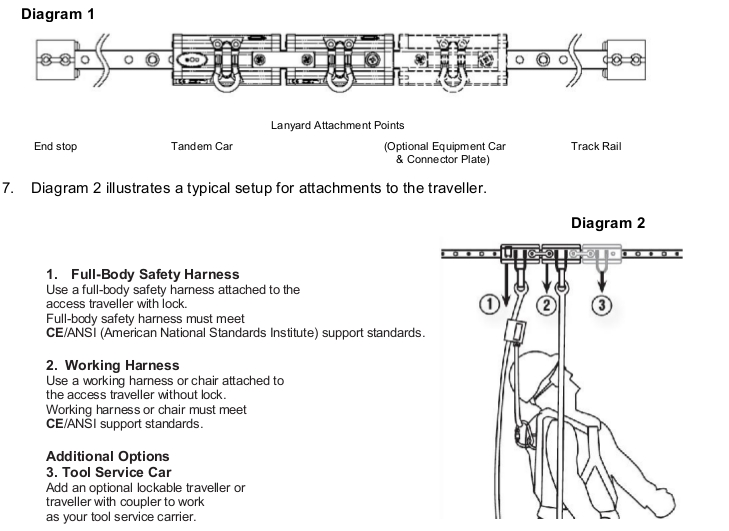
Full-body safety harness; use a full-body safety harness attached to the access traveller with lock. Full-body safety harness must meet UKCA mark or an alternative standard which provides equivalent levels of safety, suitability and fitness for purpose when in use.
Working Harness; use a working harness or chair attached to the access traveller without lock. Working harness or chair must meet UKCA mark or an alternative standard which provides equivalent levels of safety, suitability and fitness for purpose when in use.
Additional Options 3. Tool service car; add an optional lockable traveller or traveller with coupler to work as your tool service carrier.
ANNEX 3
REQUIREMENTS FOR SINGLE PERSON SYSTEMS
The system used should be tested, certified and approved to EN 795:2012, Class D (or any subsequent revision). This ensures the system has passed tests for general requirements, static (1200kg for 3 minutes) and dynamic (9Kn + 3Kn static for 3min) tests and corrosion resistance.
The system, full-body safety harness and fall arrester should carry the UKCA mark or an alternative standard which provides equivalent levels of safety, suitability and fitness for purpose when in use and comply with EN standards.
The systems described are to carry no more than one person and total weight (person, clothes and tools) should not exceed 100kg.
Trackways may be fitted at any orientation between horizontal facing down (0°) and vertical (90°) if this brings the shackle in contact with the car.
Stainless steel countersunk through-bolts (i.e. without a nut) to be utilised at a maximum 100mm spacing and in accordance with the manufacturer's requirements. Equivalent arrangements could also be considered. Alternative fixing options for steel or aluminium hulls must be appropriate to the hull design, proof tested as per Annex 2 and installed to manufacturers recommendations. Full details of the installation including method of anchorage and supporting technical documentation (fixing certification) must be issued on completion of every installation; other materials would require doubling plates to achieve equivalent strength.
Drawings of proposed installation to be submitted to the MCA, Class or the Certifying Authority, as appropriate for approval.
Installation testing to be witnessed by MCA, Class or Certifying Authority, as appropriate. This is to test whether the track comes away from the base when a load is applied.
Where fastenings are not through steelwork, the static and dynamic tests to be repeated on a sample. This sample should not be off the yacht or vessel.
We recommend that if you want to be compliant with EN795:2012 the installation needs to be test as stated below:
Installation testing:
This test objective is to ensure that the system has been installed correctly in practice and remains sound as it ages.
We recommend that each rail is tested in at least 3 locations, typically at both ends and at any rail joint or in the middle.
Again subject to surveyor approval, each rail should be tested on installation as per:
- attach a water bag to a single car or anchoring point (where multiple cars are used each car should be subject to a loading test)
- fill to achieve a load of 600 kg
- test for 15 seconds per location
- repeat as necessary for each separate rail
This testing shall be witnessed by an approved surveyor and recorded on a suitable load test certificate which is duly endorsed by the witnessing parties.
Such testing shall be carried out along with any additional requirements specified by the system manufacturer.
On conclusion of testing the system shall be confirmed fit for use, without damage or permanent distortion
Normal safety equipment operations requires testing post-installation and then 6 monthly routine inspections with 12 monthly testings.
Further testing and inspection of the ARS should be incorporated into standard operating practices and into the safety records.
Documentation to be supplied after installation
The installation documentation provides evidence to the end uses and that the installation has been carried out properly.
The documentation should be handed over to the user and kept on hand for subsequent examinations of the device.
The Manufacturer's approval certificate (EN 795:2012, Type D), operating and maintenance instructions. should contain at least:
- address and location of installation
- name and address of installation company
- name of the person in charge of the installation
- product identification
- fixing device
Schematic installation plan
a declaration by the installer, that it is;
- installed in accordance with manufacturer's instructions
- carried out in accordance to plan
- fixed as specified
- commissioned in accordance with manufacturer's instructions
- test certificate as witnessed by the MCA or their delegate